Formlabs Expands into Metal Part Casting with New Resin
- 列印專門店 瑞思3D
- Sep 9, 2024
- 3 min read
Source: Formlabs
Author: Carolyn Schwaar
Published on September 6, 2024

A new material and workflow for industrial investment casting foundries aims to lower the cost and labor of making patterns and molds.
Making patterns, cores and molds for casting metal is among the traditional manufacturing processes that 3D printing is ideal to replace. CNC machining is the most common industrial method for these parts. It works with various plastics and metals, but 3D printing patterns in a growing range of special casting materials is a faster and less expensive method with equal accuracy.
Another reason printing molds and patterns, instead of machining them, is becoming more widely adopted in various industries is because it can produce patterns in geometries, such as internal channels and thin walls, that are difficult or impossible to machine or require time-consuming secondary assembly or milling to get to the final product, such as adding gating features.
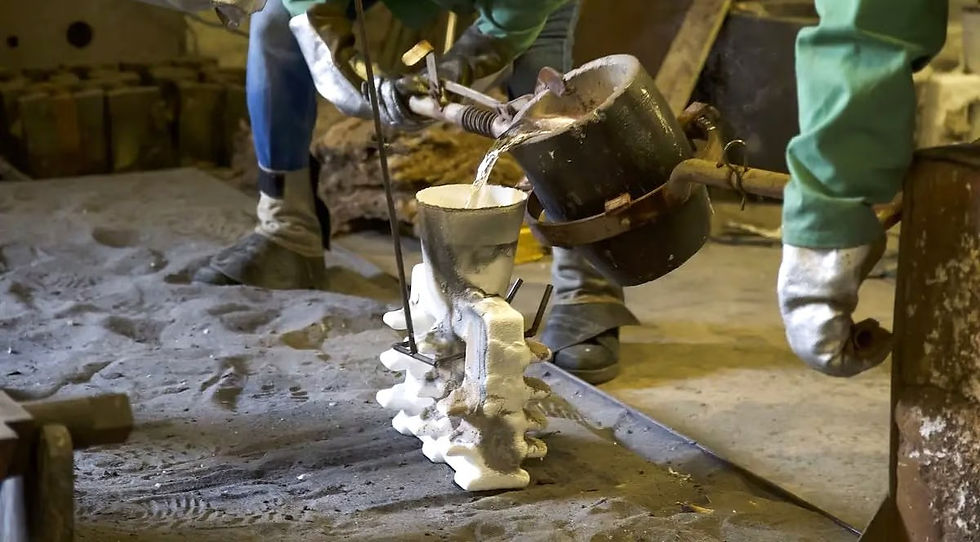
Although 3D printing has always had accuracy, advancements in materials are driving more adoption for investment casting applications.
Formlabs, the resin 3D printer and material maker, this week launched a new casting material called Clear Cast Resin designed to help foundries produce molds and patterns more efficiently.
The new Clear Cast Resin is aimed at enabling foundries to cast designs in-house with least cost and turnaround time, plus iterating flexibility. The material is accurate within 0.25 mm, delivering reliable casting shells with minimal cracking, Formlabs says.
One early adopter of the resin is Alabama-based precision foundry Diversified Metalsmiths. Its VP of Technology John Farr says: “The Clear Cast parts slotted straight into the workflow, [and] the amount of time saved with 3D printing where I push a button and go off to do something else, then skip the machining and hand-work after the cast, will make up for the cost of 3D printed patterns.”
After requesting sample parts from Formlabs, Farr found that the Form 3L and Clear Cast Resin were accessibly priced for a smaller foundry like theirs and made an effective replacement for their outsourced PMMA patterns. “They didn’t need to change burnout temperatures, slurry formulation, or part design,” according to Formlabs. Creating the impeller pattern shown below in Clear Cast Resin with the Formlabs workflow cost Diversified Metalsmiths only $80 for materials and labor, compared to their previous outsourcing costs of $300, the company says.

Just because a material will melt at 400ºC, like PLA, doesn’t mean it’s right for creating investment casting patterns. Some materials may have additives that could leave behind a residue or particles in the mold. Specially made materials for casting typically boast a clean burnout and low ash residue.
Formlabs has experience in producing photopolymers with low coefficient of thermal expansion (CTE) and clean burnout. Its castable wax resins were created for the jewelry industry, but are too weak to be used for the larger, thicker, and more structurally robust parts necessary for industrial metalsmithing.
The new Clear Cast Resin burns out in two hours at 700 °C – 900 °C. It’s compatible with Formlabs’ Form 3 and Form 4 SLA 3D printers and retails for $149 per liter.

Formlabs Clear Cast Resin is available in cartridges compatible with the company’s Form 3 and Form 4 resin 3D printers (Source: Formlabs)
Formlabs produced a white paper detailing the investment casting pattern and mold-making process used at its beta testers’ foundries.
source: Formlabs and all3dp
Comments